The human brain may become a "battlefield" in future wars, including "pharmacological land mines" and drones directed by mind control, a new report has predicted. In a report commissioned by the US Defence Intelligence Agency, leading scientists were asked to examine how a greater understanding of the brain over the next 20 years is likely to drive the development of new medicines and technologies. According to the Guardian newspaper, US intelligence officials were told that rapid advances in neuroscience could have a dramatic impact on national security and the way in which future wars are fought. According to the report, they found several areas in which progress could have a profound impact, including behaviour-altering drugs, scanners that can interpret a person's state of mind and devices capable of boosting senses such as hearing and vision. Bullets may be replaced with "pharmacological land mines" that release drugs to incapacitate soldiers on contact, while scanners and other electronic devices could be developed to identify suspects from their brain activity and even disrupt their ability to tell lies, the report says. Greater understanding of the brain's workings is also expected to usher in new devices that link directly to the brain, either to allow operators to control machinery with their minds, such as flying unmanned reconnaissance drones, or to boost their natural senses. "Experiments indicate that the advantages of these devices are such that human operators will be greatly enhanced for things like photo reconnaissance and so on," Kit Green, the chairman of the report committee, was quoted as saying by the British daily on Thursday.
Sunday, August 17, 2008
Thursday, August 14, 2008
TECHNICAL ARTICLE
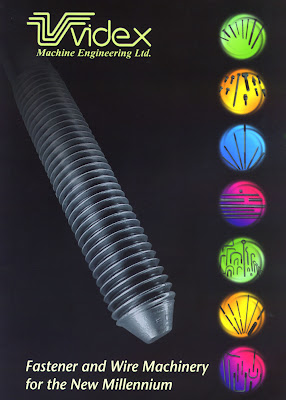
Closed Frame Thread Rollers
In recent years, planetary thread rollers have been adapted to reduce labor and handling, roll smaller batches of higher-quality parts and to allow use by less skilled operators.
The planetary thread rolling system has come a long way since the 1970s and 1980s. In the past, the planetary system was used for rolling commercial and industrial products not requiring high dimensional and quality standards. These products are now made in China and other countries that offer reasonable quality and inexpensive prices, allowing a wider range of customers to purchase products that were once out of reach.
The fact that many standard fasteners are no longer manufactured n the USA and the rest of the western world has created a positive move forward in parts development and R&D of processes, which has resulted in more sophisticated and better quality products. The planetary system that was once used for rolling simple parts is now evolving to accommodate the changing needs of the fastener industry. In the last six years, Videx has been concentrating on developing and adapting this system to reduce labor and handling, roll smaller batches of high-quality parts and to allow less skilled operators to recall machine settings with ease.
Quality of Thread
Thread quality was the major issue and the key to the success of the Videx VA line of thread rollers. Videx has identified a problem in the uncontrolled feed of the blanks into the thread rolling dies in the planetary system. It has developed anew feed system that squares and feeds the blanks while they are already in motion and turns with the rotary die at the same linear speed. n the new system, the blanks move farther before they are fed in between the thread rolling dies. A newly developed feed system has a longer stroke and is more precise with a uniform feed force along the feed stroke. To achieve all these requirements, we eliminated the feed slide and the spring that required constant maintenance to keep them accurate. In the new system, the blanks are fed by a pivot arm and a pneumatic piston. This system is virtually maintenance free. The thread quality achieved with the above system enabled us to develop a few models for the automotive and aero space industries, all based on high quality requirements.
Dual-Spindle Thread Rollers: The first machine designed is a thread roller with two spindles (VA-K), for rolling knurls and threads on wheel bolts in two consecutive operations, done one after the other. The VA-20-K has two rolling stations, capable of performing two rolling operations on the same part. The machine can be used for the following applications:
• Knurl and thread rolling of wheel bolts
• Knurl and thread rolling of socket head cap screws.
• Chamfer, groove and thread standard and long bolts.
The two rolling heads are independently set and matched, eliminating any influence of one rolling operation on the other. The two rolling operations are done one after the other, while the blanks stay oriented in the feed rails, after the first rolling station operation and prior to the second rolling operation. This construction assures that there is no damage to the thread.
The VA-20-K dual head thread rollers solve problems such as the following:
• Separate operations assure a better quality of each rolled operation. It also helps to better control the separate operations and the tooling used.
• Speed achieved is higher than in any other system because the second operation does not slow the machine.
• By saving on handling, the VA-20-K eliminates the possibility of mixing parts, such as heat-treated parts with non-heat-treated parts.
• System allows rolling with inexpensive tooling, while having full control over the quality of each rolling operation. When a tool has to be replaced, it can be done in minutes.
The production rate for example, on standard wheel bolts is 320 to 500 ppm. Both threading stations havehydraulic clamping of thread rolling dies, zero-taper device for parallel threads and micrometric thread pressure screws. Other standard features include AC speed controller, automatic air shutoff and dual operator control panel on both sides of the machine for convenient and safe operation. The control panel at the back is also used when setting up the feeder.
T-Bolt Thread Rollers: Another model that was developed as a consequence of the new feed system was the VA-T series for rolling T-bolts. These thread rolling machines incorporate special T-bolt feeders that were developed in the USA. Combined with the long stroke feed mechanism, this special feeder allows the feeding of T-bolts one by one into the thread rolling dies at speeds of 100 to 200 ppm
Thread Rollers for Pre-Hardened Fasteners: The real breakthrough in the furthering of the planetary system was achieved last year. Based on the increasing market need to roll harder materials and longer threads, Videx developed a line of machinery with 200 mm (8") and 300 mm (12") thread length capacity To overcome deflection problems, we used a technique of a closed structure, creating a closed frame between the segment die and the rotary die. This construction is similar to the construction of a two-roll machine, and enables Videx to offer machines with long thread capacity, that roll perfectly parallel threads on any length of parts and any material hardness. An unexpected result of the supported spindle construction, which was discovered by customers, was a considerable increase in the life of a thread rolling die especially when rolling pre-hardened parts, between 25 Rc and 36 Rc .This improvement in die life is now opening new opportunities for the planetary system, and Videx has decided to offer the closed structure thread rollers as an additional line to its commercial thread rollers. This line was demonstrated for the first time at the wire 2002 show, rolling pre-hardened M-14threads at a rate of 250 ppm The closed structure thread rollers can be used for the following applications:
• Thread rolling of pre-hardened fasteners.
• Straightening/rolling of long screws after heat treating.
• Thread rolling of long bolts to 350 mm (13.7") under head.
• Rolling of hard to roll forms such as Acme threads.
• Re-rolling of hardened fasteners.
• Feeding/rolling of hard to feed and grip parts like flanged bolts or parts with an upset under or above the head.
• Double-end thread rolling of headed parts under or above the head.
Dual Station (Single Spindle) Thread Rollers: The next step in machine design was the creation of a thread roller with a supported spindle and two rolling stations. This machine was designed for an American company that was looking for a thread roller that can roll long parts, with a thread and a chamfer above the head
Emphasis
Videx Machine Engineering Ltd., offers fully automated machines for the production of a variety of bolts and studs including magazine-feed thread rollers and bending machines. Also offered are planetary thread and form rollers for headed parts, various bolts, pipe plugs, etc. as well as planetary thread rolling dies. Videx also provides straightening and cutoff machines for short and long parts, construction steel and scaled wire models. designed to roll T-bolts, long screws and standard screws. The machine’s two rolling stations are mounted at a fixed distance from each other. The upper station accepts work pieces which are rolled above the head and the bottom station accepts standard screws, T-Bolts and long parts that are supported on the upper station and are rolled in the bottom station. The machine is equipped with two sets of feed rails and two floating feed arms, that can be positioned anywhere along the introduction shaft, for feeding long blanks on both sides at the same time. This feature is especially important when rolling long parts that should be fed both in the thread area and in the head area. The two rolling stations are independently set. Each one of the rolling stations has a separate thread pressure adjustment with hydraulic clamping and micrometric screws.
Additionally, the double station (single spindle) thread rolling machine can be equipped with a chamfer rolling attachment upon request of the customer. The VA line is also equipped with automatic air shutoff systems, that turn off the air supply to the feeder when it is not working and to the feed rails when the machine is not operating.
In Conclusion
The thread rolling world is in transition, with higher quality demands in many industries and tighter profit margins. In addition to the recent technological advantages, the prices of these machines have been kept highly affordable to protect your bottom line. For more details on planetary thread rolling machines
The planetary thread rolling system has come a long way since the 1970s and 1980s. In the past, the planetary system was used for rolling commercial and industrial products not requiring high dimensional and quality standards. These products are now made in China and other countries that offer reasonable quality and inexpensive prices, allowing a wider range of customers to purchase products that were once out of reach.
The fact that many standard fasteners are no longer manufactured n the USA and the rest of the western world has created a positive move forward in parts development and R&D of processes, which has resulted in more sophisticated and better quality products. The planetary system that was once used for rolling simple parts is now evolving to accommodate the changing needs of the fastener industry. In the last six years, Videx has been concentrating on developing and adapting this system to reduce labor and handling, roll smaller batches of high-quality parts and to allow less skilled operators to recall machine settings with ease.
Quality of Thread
Thread quality was the major issue and the key to the success of the Videx VA line of thread rollers. Videx has identified a problem in the uncontrolled feed of the blanks into the thread rolling dies in the planetary system. It has developed anew feed system that squares and feeds the blanks while they are already in motion and turns with the rotary die at the same linear speed. n the new system, the blanks move farther before they are fed in between the thread rolling dies. A newly developed feed system has a longer stroke and is more precise with a uniform feed force along the feed stroke. To achieve all these requirements, we eliminated the feed slide and the spring that required constant maintenance to keep them accurate. In the new system, the blanks are fed by a pivot arm and a pneumatic piston. This system is virtually maintenance free. The thread quality achieved with the above system enabled us to develop a few models for the automotive and aero space industries, all based on high quality requirements.
Dual-Spindle Thread Rollers: The first machine designed is a thread roller with two spindles (VA-K), for rolling knurls and threads on wheel bolts in two consecutive operations, done one after the other. The VA-20-K has two rolling stations, capable of performing two rolling operations on the same part. The machine can be used for the following applications:
• Knurl and thread rolling of wheel bolts
• Knurl and thread rolling of socket head cap screws.
• Chamfer, groove and thread standard and long bolts.
The two rolling heads are independently set and matched, eliminating any influence of one rolling operation on the other. The two rolling operations are done one after the other, while the blanks stay oriented in the feed rails, after the first rolling station operation and prior to the second rolling operation. This construction assures that there is no damage to the thread.
The VA-20-K dual head thread rollers solve problems such as the following:
• Separate operations assure a better quality of each rolled operation. It also helps to better control the separate operations and the tooling used.
• Speed achieved is higher than in any other system because the second operation does not slow the machine.
• By saving on handling, the VA-20-K eliminates the possibility of mixing parts, such as heat-treated parts with non-heat-treated parts.
• System allows rolling with inexpensive tooling, while having full control over the quality of each rolling operation. When a tool has to be replaced, it can be done in minutes.
The production rate for example, on standard wheel bolts is 320 to 500 ppm. Both threading stations havehydraulic clamping of thread rolling dies, zero-taper device for parallel threads and micrometric thread pressure screws. Other standard features include AC speed controller, automatic air shutoff and dual operator control panel on both sides of the machine for convenient and safe operation. The control panel at the back is also used when setting up the feeder.
T-Bolt Thread Rollers: Another model that was developed as a consequence of the new feed system was the VA-T series for rolling T-bolts. These thread rolling machines incorporate special T-bolt feeders that were developed in the USA. Combined with the long stroke feed mechanism, this special feeder allows the feeding of T-bolts one by one into the thread rolling dies at speeds of 100 to 200 ppm
Thread Rollers for Pre-Hardened Fasteners: The real breakthrough in the furthering of the planetary system was achieved last year. Based on the increasing market need to roll harder materials and longer threads, Videx developed a line of machinery with 200 mm (8") and 300 mm (12") thread length capacity To overcome deflection problems, we used a technique of a closed structure, creating a closed frame between the segment die and the rotary die. This construction is similar to the construction of a two-roll machine, and enables Videx to offer machines with long thread capacity, that roll perfectly parallel threads on any length of parts and any material hardness. An unexpected result of the supported spindle construction, which was discovered by customers, was a considerable increase in the life of a thread rolling die especially when rolling pre-hardened parts, between 25 Rc and 36 Rc .This improvement in die life is now opening new opportunities for the planetary system, and Videx has decided to offer the closed structure thread rollers as an additional line to its commercial thread rollers. This line was demonstrated for the first time at the wire 2002 show, rolling pre-hardened M-14threads at a rate of 250 ppm The closed structure thread rollers can be used for the following applications:
• Thread rolling of pre-hardened fasteners.
• Straightening/rolling of long screws after heat treating.
• Thread rolling of long bolts to 350 mm (13.7") under head.
• Rolling of hard to roll forms such as Acme threads.
• Re-rolling of hardened fasteners.
• Feeding/rolling of hard to feed and grip parts like flanged bolts or parts with an upset under or above the head.
• Double-end thread rolling of headed parts under or above the head.
Dual Station (Single Spindle) Thread Rollers: The next step in machine design was the creation of a thread roller with a supported spindle and two rolling stations. This machine was designed for an American company that was looking for a thread roller that can roll long parts, with a thread and a chamfer above the head
Emphasis
Videx Machine Engineering Ltd., offers fully automated machines for the production of a variety of bolts and studs including magazine-feed thread rollers and bending machines. Also offered are planetary thread and form rollers for headed parts, various bolts, pipe plugs, etc. as well as planetary thread rolling dies. Videx also provides straightening and cutoff machines for short and long parts, construction steel and scaled wire models. designed to roll T-bolts, long screws and standard screws. The machine’s two rolling stations are mounted at a fixed distance from each other. The upper station accepts work pieces which are rolled above the head and the bottom station accepts standard screws, T-Bolts and long parts that are supported on the upper station and are rolled in the bottom station. The machine is equipped with two sets of feed rails and two floating feed arms, that can be positioned anywhere along the introduction shaft, for feeding long blanks on both sides at the same time. This feature is especially important when rolling long parts that should be fed both in the thread area and in the head area. The two rolling stations are independently set. Each one of the rolling stations has a separate thread pressure adjustment with hydraulic clamping and micrometric screws.
Additionally, the double station (single spindle) thread rolling machine can be equipped with a chamfer rolling attachment upon request of the customer. The VA line is also equipped with automatic air shutoff systems, that turn off the air supply to the feeder when it is not working and to the feed rails when the machine is not operating.
In Conclusion
The thread rolling world is in transition, with higher quality demands in many industries and tighter profit margins. In addition to the recent technological advantages, the prices of these machines have been kept highly affordable to protect your bottom line. For more details on planetary thread rolling machines
Sunday, August 10, 2008
WELDING TECHNOLOGY
Friday, June 20, 2008
Steam power
The development of the stationary steam engine was an essential early element of the Industrial Revolution; however, for most of the period of the Industrial Revolution, the majority of industries still relied on wind and water power as well as horse and man-power for driving small machines.
The first real attempt at industrial use of steam power was due to Thomas Savery in 1698. He constructed and patented in London a low-lift combined vacuum and pressure water pump, that generated about one horsepower (hp) and was used as in numerous water works and tried in a few mines (hence its "brand name", The miner's Friend), but it was not a success since it was limited in pumping height and prone to boiler explosions.
Newcomen's steam powered atmospheric engine was the first practical engine. Subsequent steam engines were to power the Industrial Revolution
The first safe and successful steam power plant was introduced by Thomas Newcomen from 1719. Newcomen apparently conceived his machine quite independently of Savery, but as the latter had taken out a very wide-ranging patent, Newcomen and his associates were obliged to come to an arrangement with him, marketing the engine until 1733 under a joint patent.[26] Newcomen's engine appears to have been based on Papin's experiments carried out 30 years earlier, and employed a piston and cylinder, one end of which was open to the atmosphere above the piston. Steam just above atmospheric pressure (all that the boiler could stand) was introduced into the lower half of the cylinder beneath the piston during the gravity-induced upstroke; the steam was then condensed by a jet of cold water injected into the steam space to produce a partial vacuum; the pressure differential between the atmosphere and the vacuum on either side of the piston displaced it downwards into the cylinder, raising the opposite end of a rocking beam to which was attached a gang of gravity-actuated reciprocating force pumps housed in the mineshaft. The engine's downward power stroke raised the pump, priming it and preparing the pumping stroke. At first the phases were controlled by hand, but within ten years an escapement mechanism had been devised worked by of a vertical plug tree suspended from the rocking beam which rendered the engine self-acting.
A number of Newcomen engines were successfully put to use in Britain for draining hitherto unworkable deep mines, with the engine on the surface; these were large machines, requiring a lot of capital to build, and produced about 5 hp (3.7 kW). They were extremely inefficient by modern standards, but when located where coal was cheap at pit heads, opened up a great expansion in coal mining by allowing mines to go deeper. Despite their disadvantages, Newcomen engines were reliable and easy to maintain and continued to be used in the coalfields until the early decades of the nineteenth century. By 1729, when Newcomen died, his engines had spread (first) to Hungary in 1722 ,Germany, Austria, and Sweden. A total of 110 are known to have been built by 1733 when the joint patent expired, of which 14 were abroad. In the 1770s, the engineer John Smeaton built some very large examples and introduced a number of improvements. A total of 1,454 engines had been built by 1800.
James Watt
A fundamental change in working principles was brought about by James Watt. With the close collaboration Matthew Boulton, he had succeeded by 1778 in perfecting his steam engine, which incorporated a series of radical improvements, notably the closing off of the upper part of the cylinder thereby making the low pressure steam drive the top of the piston instead of the atmosphere, use of a steam jacket and the celebrated separate steam condenser chamber. All this meant that a more constant temperature could be maintained in the cylinder and that engine efficiency no longer varied according to atmospheric conditions. These improvements increased engine efficiency by a factor of about five, saving 75% on coal costs.
Nor could the atmospheric engine be easily adapted to drive a rotating wheel, although Wasborough and Pickard did succeed in doing so towards 1780. However by 1783 the more economical Watt steam engine had been fully developed into a double-acting rotative type, which meant that it could be used to directly drive the rotary machinery of a factory or mill. Both of Watt's basic engine types were commercially very successful, and by 1800, the firm Boulton & Watt had constructed 496 engines, with 164 driving reciprocating pumps, 24 serving blast furnaces, and 308 powering mill machinery; most of the engines generated from 5 to 10 hp (7.5 kW).
The development of machine tools, such as the lathe, planing and shaping machines powered by these engines, enabled all the metal parts of the engines to be easily and accurately cut and in turn made it possible to build larger and more powerful engines.
Until about 1800, the most common pattern of steam engine was the beam engine, built as an integral part of a stone or brick engine-house, but soon various patterns of self-contained portative engines (readily removable, but not on wheels) were developed, such as the table engine. Towards the turn of the 19th century, the Cornish engineer Richard Trevithick, and the American, Oliver Evans began to construct higher pressure non-condensing steam engines, exhausting against the atmosphere. This allowed an engine and boiler to be combined into a single unit compact enough to be used on mobile road and rail locomotives and steam boats.
In the early 19th century after the expiration of Watt's patent, the steam engine underwent many improvements by a host of inventors and engineers.
The first real attempt at industrial use of steam power was due to Thomas Savery in 1698. He constructed and patented in London a low-lift combined vacuum and pressure water pump, that generated about one horsepower (hp) and was used as in numerous water works and tried in a few mines (hence its "brand name", The miner's Friend), but it was not a success since it was limited in pumping height and prone to boiler explosions.
Newcomen's steam powered atmospheric engine was the first practical engine. Subsequent steam engines were to power the Industrial Revolution
The first safe and successful steam power plant was introduced by Thomas Newcomen from 1719. Newcomen apparently conceived his machine quite independently of Savery, but as the latter had taken out a very wide-ranging patent, Newcomen and his associates were obliged to come to an arrangement with him, marketing the engine until 1733 under a joint patent.[26] Newcomen's engine appears to have been based on Papin's experiments carried out 30 years earlier, and employed a piston and cylinder, one end of which was open to the atmosphere above the piston. Steam just above atmospheric pressure (all that the boiler could stand) was introduced into the lower half of the cylinder beneath the piston during the gravity-induced upstroke; the steam was then condensed by a jet of cold water injected into the steam space to produce a partial vacuum; the pressure differential between the atmosphere and the vacuum on either side of the piston displaced it downwards into the cylinder, raising the opposite end of a rocking beam to which was attached a gang of gravity-actuated reciprocating force pumps housed in the mineshaft. The engine's downward power stroke raised the pump, priming it and preparing the pumping stroke. At first the phases were controlled by hand, but within ten years an escapement mechanism had been devised worked by of a vertical plug tree suspended from the rocking beam which rendered the engine self-acting.
A number of Newcomen engines were successfully put to use in Britain for draining hitherto unworkable deep mines, with the engine on the surface; these were large machines, requiring a lot of capital to build, and produced about 5 hp (3.7 kW). They were extremely inefficient by modern standards, but when located where coal was cheap at pit heads, opened up a great expansion in coal mining by allowing mines to go deeper. Despite their disadvantages, Newcomen engines were reliable and easy to maintain and continued to be used in the coalfields until the early decades of the nineteenth century. By 1729, when Newcomen died, his engines had spread (first) to Hungary in 1722 ,Germany, Austria, and Sweden. A total of 110 are known to have been built by 1733 when the joint patent expired, of which 14 were abroad. In the 1770s, the engineer John Smeaton built some very large examples and introduced a number of improvements. A total of 1,454 engines had been built by 1800.
James Watt
A fundamental change in working principles was brought about by James Watt. With the close collaboration Matthew Boulton, he had succeeded by 1778 in perfecting his steam engine, which incorporated a series of radical improvements, notably the closing off of the upper part of the cylinder thereby making the low pressure steam drive the top of the piston instead of the atmosphere, use of a steam jacket and the celebrated separate steam condenser chamber. All this meant that a more constant temperature could be maintained in the cylinder and that engine efficiency no longer varied according to atmospheric conditions. These improvements increased engine efficiency by a factor of about five, saving 75% on coal costs.
Nor could the atmospheric engine be easily adapted to drive a rotating wheel, although Wasborough and Pickard did succeed in doing so towards 1780. However by 1783 the more economical Watt steam engine had been fully developed into a double-acting rotative type, which meant that it could be used to directly drive the rotary machinery of a factory or mill. Both of Watt's basic engine types were commercially very successful, and by 1800, the firm Boulton & Watt had constructed 496 engines, with 164 driving reciprocating pumps, 24 serving blast furnaces, and 308 powering mill machinery; most of the engines generated from 5 to 10 hp (7.5 kW).
The development of machine tools, such as the lathe, planing and shaping machines powered by these engines, enabled all the metal parts of the engines to be easily and accurately cut and in turn made it possible to build larger and more powerful engines.
Until about 1800, the most common pattern of steam engine was the beam engine, built as an integral part of a stone or brick engine-house, but soon various patterns of self-contained portative engines (readily removable, but not on wheels) were developed, such as the table engine. Towards the turn of the 19th century, the Cornish engineer Richard Trevithick, and the American, Oliver Evans began to construct higher pressure non-condensing steam engines, exhausting against the atmosphere. This allowed an engine and boiler to be combined into a single unit compact enough to be used on mobile road and rail locomotives and steam boats.
In the early 19th century after the expiration of Watt's patent, the steam engine underwent many improvements by a host of inventors and engineers.
Thursday, June 19, 2008
Technology and Leisure in Britain after 1850
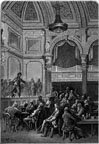
The railway company was eventually persuaded in the late 1860s, after pressure from the respectable residents, to effect a discrete revision of the excursion traffic. The price of the day return ticket was raised which together with the growth of attractive alternative destinations on the coast improved greatly the class of people who patronised the town in the summer months.
The demand for seaside resorts after 1850 either increased the size of or developed new coastal towns. Workers in Yorkshire textile industries motivated the development of Blackpool as popular seaside facilities with evident commercial potential.
New technology like the steam press caused an increase in the consumption of pulp fiction, mainly purchased by the working classes, and cheap newspaper further advanced leisure publicity. Similarly, the invention of the bicycle not only enabled excursions and cheap modes of transport, it had a great effect upon women. Their use of the bicycle as an accepted leisure practice freed many women from restrictive clothing. The bicycle also led to calls for the improvement and building of better roads, which in turn affected the Victorian Town.
A Tight-rope Walker and Music Hall from Jerrold and Doré's London
[Click on thumbnails for larger images.]
Commercialisation of leisure by the latter quarter of the nineteenth century became an increasingly influential factor. Music Halls roots in the crude localised "free and easies" were often commented upon by moral reformers (usually in the press), for to them it represented all the worst accesses of leisure — namely, drunkenness, obscenity and sensuality. George Morgan's Canterbury Hall was the first large-scale music hall, and halls grew in splendour and sought to attract a more prosperous class. With the eventual patronage of a better clientele the music hall invaded the suburbs, and the businessmen Moss and Stoll greatly advanced this trend. Here the press again was used to attract potential customers, the hegemony of acts began to develop and the concept of the star was born. Charles Chaplain and Gracie Fields are both examples of this new star phenomena, soon to be projected to new highest by the cinema, which in turn developed from the music hall. The publication of popular songs became big business, employing many lower-middle-class song writers. By the 1880s the music hall had become so respectable that in many towns it rivaled the town hall and other civic buildings. Another sign of the increasing the respectabilty of music hall and theatre appears in the fact that that churches often built extensions to hold amateur dramatics.
The latter nineteenth century commercialisation and mass production produced many familiar commodities: the post card, fish and chips, ice-cream, cigarettes, mineral water and the teacup. The Victorian town was the mould which contained all these fermenting elements, both reshaping leisure and being reshaped by this process of leisure revolution.
The Development of Leisure in Britain, 1700-1850
The Development of Leisure in Britain after 1850
References
Bailey, P.C. Music Hall The Business of Pleasure. Milton Keynes: Open University Press. 1986.
Bailey, P.C. Leisure, Culture and the Historian. Leisure Studies 8 E.& F.N. Spon Ltd. 1989. Pp. 109-122.
Cunningham, H. Leisure in the Industrial Revolution c1780-c1880. London: Croom Helm. 1980.
Cunningham, H. Leisure, in The Working Class England, 1875-1914. London: Croom Helm. 1985.
Leader, A. Culture Theory and Popular Culture. Brighton: Harvester/Wheatshed. 1974.
Lowerson, J.& Myerscough, J. Time to Spare in Victorian England. Harvester Press. 1977.
Robbinson, K. Nineteenth-Century Britain. Oxford: Oxford University Press. 1988.
Thompson, E.P. Customs in Common. Chapter 8 "Rough Music." Pp. 497-531.
Walton, J.K. The English Seaside Resort. London: St. Martins Press. 1983.
Wednesday, June 18, 2008
Lifelong Learning
Educating Mom
Why single parents may be the most crucial undergraduate demographic
Why single parents may be the most crucial undergraduate demographic
After dropping out of Florida Atlantic University in 2002, Vivian Vo's decision to return to the classroom five years later was fueled by the very thing that made her leave in the first place -- her daughter. Completing her bachelor's degree in fashion design and marketing from American Intercontinental University in October 2007, Vo landed a position as a design assistant for uniform supplier Cintas before she had turned the tassel."The major reason I left school was because of my pregnancy. ... I chose to go back in order to provide a better future for my daughter and to become a good teacher for her," said the 26-year-old mother. Vo isn't the only single mom dedicated to conquering employment, education and child rearing in a single bound. Despite skyrocketing tuition costs and federal financial aid cuts, the Department of Education reports that there are twice as many single parents enrolled in higher education as there were just 10 years ago.
The spike in single-parent grads can be, in part, chalked up to necessity. As the pay gap between workers with college degrees and those without steadily widens, an increasing number of single parents simply have to gain higher-education credentials in order to stay afloat. Unfortunately, many still sink, and many of them are women. A 2006 census poll shows that more than half of all U.S. families currently living below the poverty line are headed by single moms. More parents, including Vo, are finding that cracking the books is one of the surest ways to gain financial security. A second development, said Jill Sullivan, director of the Keys to Degrees program at Endicott College in Beverly, Mass., is that universities and colleges are slowly beginning to recognize single moms as an underserved population. "[Single-parent students are] trying to balance work and going to school and paying for day care and it's hard," Sullivan said. "College is usually the first thing that these parents would give up and we're trying to help."
Keys to Degrees is one of a handful of residential college programs nationwide aimed at keeping single parents in the classroom. In addition to receiving specialized child-friendly on-campus housing, free day care and a scholarship worth up to half of the yearly tuition, Endicott's nine Keys to Degrees parent-students also receive access to bimonthly parent support meetings and playgroups for the children. Single-parent programs like Endicott's and the one at Champlain College in Burlington, Vt., aim to make an impact that extends far beyond both the grads and their immediate families. A recent survey conducted by American Intercontinental University shows that 80 percent of single moms between the ages of 18 and 29 would like to go back to the books. However, family and financial obstacles prevent all but 13 percent from getting there
Sullivan stresses the idea that by helping these students finish school, the schools are helping them gain financial independence that might not come easy without the education. She scoffs at the stereotype of the welfare-dependent single parent. "If the state would help them get through the education system, they're off the system after four years because they'll have the degree," she said. For those that do make it past the admissions gate, the outlook is promising according to Sue Lawrence, executive director of the Jeannette Rankin Foundation, a nonprofit agency based in Athens, Ga., that provides scholarships to women aged 35 and above.
"Once they actually get into the classroom, we know that women with dependents are very serious about their studies," said Lawrence. "These women aren't going to school so that they can figure out what they want to be in life. They go because they very passionately want to provide for their families and give back to their communities." Giving back may be precisely what makes the single mother such a critical demographic. Besides breaking the cycle of poverty, studies show that single moms who return to school frequently gravitate toward careers in areas such as education, health care and social work -- fields that are anticipated to face a critical worker shortage within the next 10 years. "I'd say that 75 to 80 percent of the women we award scholarships to choose a field like teaching or legal services, a field where they can make a contribution," said Lawrence. "These women want careers that are helping society in some way because it's not about them, they're not just going to school for themselves."
Whether it's staying above the poverty line, filling an upcoming labor gap or simply being a role model for their children, two things about single moms are clear -- there's a lot riding on their career choices and the odds are against them. For Vo, those factors are only further proof that her choice to invest in her education was the right one. Vo makes it clear that it was hard work, but a valuable investment: "There are days that you're working and you're stressed, but in the end it's worth it because you're working towards a goal that's going to provide a much better future."
The spike in single-parent grads can be, in part, chalked up to necessity. As the pay gap between workers with college degrees and those without steadily widens, an increasing number of single parents simply have to gain higher-education credentials in order to stay afloat. Unfortunately, many still sink, and many of them are women. A 2006 census poll shows that more than half of all U.S. families currently living below the poverty line are headed by single moms. More parents, including Vo, are finding that cracking the books is one of the surest ways to gain financial security. A second development, said Jill Sullivan, director of the Keys to Degrees program at Endicott College in Beverly, Mass., is that universities and colleges are slowly beginning to recognize single moms as an underserved population. "[Single-parent students are] trying to balance work and going to school and paying for day care and it's hard," Sullivan said. "College is usually the first thing that these parents would give up and we're trying to help."
Keys to Degrees is one of a handful of residential college programs nationwide aimed at keeping single parents in the classroom. In addition to receiving specialized child-friendly on-campus housing, free day care and a scholarship worth up to half of the yearly tuition, Endicott's nine Keys to Degrees parent-students also receive access to bimonthly parent support meetings and playgroups for the children. Single-parent programs like Endicott's and the one at Champlain College in Burlington, Vt., aim to make an impact that extends far beyond both the grads and their immediate families. A recent survey conducted by American Intercontinental University shows that 80 percent of single moms between the ages of 18 and 29 would like to go back to the books. However, family and financial obstacles prevent all but 13 percent from getting there
Sullivan stresses the idea that by helping these students finish school, the schools are helping them gain financial independence that might not come easy without the education. She scoffs at the stereotype of the welfare-dependent single parent. "If the state would help them get through the education system, they're off the system after four years because they'll have the degree," she said. For those that do make it past the admissions gate, the outlook is promising according to Sue Lawrence, executive director of the Jeannette Rankin Foundation, a nonprofit agency based in Athens, Ga., that provides scholarships to women aged 35 and above.
"Once they actually get into the classroom, we know that women with dependents are very serious about their studies," said Lawrence. "These women aren't going to school so that they can figure out what they want to be in life. They go because they very passionately want to provide for their families and give back to their communities." Giving back may be precisely what makes the single mother such a critical demographic. Besides breaking the cycle of poverty, studies show that single moms who return to school frequently gravitate toward careers in areas such as education, health care and social work -- fields that are anticipated to face a critical worker shortage within the next 10 years. "I'd say that 75 to 80 percent of the women we award scholarships to choose a field like teaching or legal services, a field where they can make a contribution," said Lawrence. "These women want careers that are helping society in some way because it's not about them, they're not just going to school for themselves."
Whether it's staying above the poverty line, filling an upcoming labor gap or simply being a role model for their children, two things about single moms are clear -- there's a lot riding on their career choices and the odds are against them. For Vo, those factors are only further proof that her choice to invest in her education was the right one. Vo makes it clear that it was hard work, but a valuable investment: "There are days that you're working and you're stressed, but in the end it's worth it because you're working towards a goal that's going to provide a much better future."
Monday, June 9, 2008
Child labour
The Industrial Revolution led to a population increase, but the chance of surviving childhood did not improve throughout the industrial revolution (although infant mortality rates were improved markedly).[30][31] There was still limited opportunity for education, and children were expected to work. Employers could pay a child less than an adult even though their productivity was comparable; there was no need for strength to operate an industrial machine, and since the industrial system was completely new there were no experienced adult labourers. This made child labour the labour of choice for manufacturing in the early phases of the Industrial Revolution between the 18th and 19th centuries.
Child labour had existed before the Industrial Revolution, but with the increase in population and education it became more visible. Before the passing of laws protecting children, many were forced to work in terrible conditions for much lower pay than their elders.
Reports were written detailing some of the abuses, particularly in the coal mines[32] and textile factories [33] and these helped to popularise the children's plight. The public outcry, especially among the upper and middle classes, helped stir change in the young workers' welfare.
Politicians and the government tried to limit child labour by law, but factory owners resisted; some felt that they were aiding the poor by giving their children money to buy food to avoid starvation, and others simply welcomed the cheap labour. In 1833 and 1844, the first general laws against child labour, the Factory Acts, were passed in England: Children younger than nine were not allowed to work, children were not permitted to work at night, and the work day of youth under the age of 18 was limited to twelve hours. Factory inspectors supervised the execution of the law. About ten years later, the employment of children and women in mining was forbidden. These laws decreased the number of child labourers; however, child labour remained in Europe up to the 20th century.
Child labour had existed before the Industrial Revolution, but with the increase in population and education it became more visible. Before the passing of laws protecting children, many were forced to work in terrible conditions for much lower pay than their elders.
Reports were written detailing some of the abuses, particularly in the coal mines[32] and textile factories [33] and these helped to popularise the children's plight. The public outcry, especially among the upper and middle classes, helped stir change in the young workers' welfare.
Politicians and the government tried to limit child labour by law, but factory owners resisted; some felt that they were aiding the poor by giving their children money to buy food to avoid starvation, and others simply welcomed the cheap labour. In 1833 and 1844, the first general laws against child labour, the Factory Acts, were passed in England: Children younger than nine were not allowed to work, children were not permitted to work at night, and the work day of youth under the age of 18 was limited to twelve hours. Factory inspectors supervised the execution of the law. About ten years later, the employment of children and women in mining was forbidden. These laws decreased the number of child labourers; however, child labour remained in Europe up to the 20th century.
Thursday, June 5, 2008
Wednesday, June 4, 2008
Machine tools
The Industrial Revolution could not have developed without machine tools, for they enabled manufacturing machines to be made. They have their origins in the tools developed in the 18th century by makers of clocks and watches and scientific instrument makers to enable them to batch-produce small mechanisms. The mechanical parts of early textile machines were sometimes called 'clock work' because of the metal spindles and gears they incorporated. The manufacture of textile machines drew craftsmen from these trades and is the origin of the modern engineering industry.
Machines were built by various craftsmen—carpenters made wooden framings, and smiths and turners made metal parts. A good example of how machine tools changed manufacturing took place in Birmingham, England, in 1830. The invention of a new machine by William Joseph Gillott, William Mitchell and James Stephen Perry allowed mass manufacture of robust, cheap steel pen nibs; the process had been laborious and expensive. Because of the difficulty of manipulating metal and the lack of machine tools, the use of metal was kept to a minimum. Wood framing had the disadvantage of changing dimensions with temperature and humidity, and the various joints tended to rack (work loose) over time. As the Industrial Revolution progressed, machines with metal frames became more common, but they required machine tools to make them economically. Before the advent of machine tools, metal was worked manually using the basic hand tools of hammers, files, scrapers, saws and chisels. Small metal parts were readily made by this means, but for large machine parts, production was very laborious and costly.
A lathe from 1911. A type of machine tool able to make other machines
Apart from workshop lathes used by craftsmen, the first large machine tool was the cylinder boring machine used for boring the large-diameter cylinders on early steam engines. The planing machine, the slotting machine and the shaping machine were developed in the first decades of the 19th century. Although the milling machine was invented at this time, it was not developed as a serious workshop tool until during the Second Industrial Revolution.
Military production had a hand in the development of machine tools. Henry Maudslay, who trained a school of machine tool makers early in the 19th century, was employed at the Royal Arsenal, Woolwich, as a young man where he would have seen the large horse-driven wooden machines for cannon boring made and worked by the Verbruggans. He later worked for Joseph Bramah on the production of metal locks, and soon after he began working on his own. He was engaged to build the machinery for making ships' pulley blocks for the Royal Navy in the Portsmouth Block Mills. These were all metal and were the first machines for mass production and making components with a degree of interchangeability. The lessons Maudslay learned about the need for stability and precision he adapted to the development of machine tools, and in his workshops he trained a generation of men to build on his work, such as Richard Roberts, Joseph Clement and Joseph Whitworth.
James Fox of Derby had a healthy export trade in machine tools for the first third of the century, as did Matthew Murray of Leeds. Roberts was a maker of high-quality machine tools and a pioneer of the use of jigs and gauges for precision workshop measurement.
Machines were built by various craftsmen—carpenters made wooden framings, and smiths and turners made metal parts. A good example of how machine tools changed manufacturing took place in Birmingham, England, in 1830. The invention of a new machine by William Joseph Gillott, William Mitchell and James Stephen Perry allowed mass manufacture of robust, cheap steel pen nibs; the process had been laborious and expensive. Because of the difficulty of manipulating metal and the lack of machine tools, the use of metal was kept to a minimum. Wood framing had the disadvantage of changing dimensions with temperature and humidity, and the various joints tended to rack (work loose) over time. As the Industrial Revolution progressed, machines with metal frames became more common, but they required machine tools to make them economically. Before the advent of machine tools, metal was worked manually using the basic hand tools of hammers, files, scrapers, saws and chisels. Small metal parts were readily made by this means, but for large machine parts, production was very laborious and costly.
A lathe from 1911. A type of machine tool able to make other machines
Apart from workshop lathes used by craftsmen, the first large machine tool was the cylinder boring machine used for boring the large-diameter cylinders on early steam engines. The planing machine, the slotting machine and the shaping machine were developed in the first decades of the 19th century. Although the milling machine was invented at this time, it was not developed as a serious workshop tool until during the Second Industrial Revolution.
Military production had a hand in the development of machine tools. Henry Maudslay, who trained a school of machine tool makers early in the 19th century, was employed at the Royal Arsenal, Woolwich, as a young man where he would have seen the large horse-driven wooden machines for cannon boring made and worked by the Verbruggans. He later worked for Joseph Bramah on the production of metal locks, and soon after he began working on his own. He was engaged to build the machinery for making ships' pulley blocks for the Royal Navy in the Portsmouth Block Mills. These were all metal and were the first machines for mass production and making components with a degree of interchangeability. The lessons Maudslay learned about the need for stability and precision he adapted to the development of machine tools, and in his workshops he trained a generation of men to build on his work, such as Richard Roberts, Joseph Clement and Joseph Whitworth.
James Fox of Derby had a healthy export trade in machine tools for the first third of the century, as did Matthew Murray of Leeds. Roberts was a maker of high-quality machine tools and a pioneer of the use of jigs and gauges for precision workshop measurement.
Chemicals
The large scale production of chemicals was an important development during the Industrial Revolution. The first of these was the production of sulphuric acid by the lead chamber process invented by the Englishman John Roebuck (James Watt's first partner) in 1746. He was able to greatly increase the scale of the manufacture by replacing the relatively expensive glass vessels formerly used with larger, less expensive chambers made of riveted sheets of lead. Instead of a few pounds at a time, he was able to make a hundred pounds (45 kg) or so at a time in each of the chambers.
The production of an alkali on a large scale became an important goal as well, and Nicolas Leblanc succeeded in 1791 in introducing a method for the production of sodium carbonate. The Leblanc process was a reaction of sulphuric acid with sodium chloride to give sodium sulphate and hydrochloric acid. The sodium sulphate was heated with limestone (calcium carbonate) and coal to give a mixture of sodium carbonate and calcium sulphide. Adding water separated the soluble sodium carbonate from the calcium sulphide. The process produced a large amount of pollution (the hydrochloric acid was initially vented to the air, and calcium sulphide was a useless waste product). Nonetheless, this synthetic soda ash proved economical compared to that from burning certain plants (barilla) or from kelp, which were the previously dominant sources of soda ash,[27] and also to potash (potassium carbonate) derived from hardwood ashes.
These two chemicals were very important because they enabled the introduction of a host of other inventions, replacing many small-scale operations with more cost-effective and controllable processes. Sodium carbonate had many uses in the glass, textile, soap, and paper industries. Early uses for sulphuric acid included pickling (removing rust) iron and steel, and for bleaching cloth.
The development of bleaching powder (calcium hypochlorite) by Scottish chemist Charles Tennant in about 1800, based on the discoveries of French chemist Claude Louis Berthollet, revolutionised the bleaching processes in the textile industry by dramatically reducing the time required (from months to days) for the traditional process then in use, which required repeated exposure to the sun in bleach fields after soaking the textiles with alkali or sour milk. Tennant's factory at St Rollox, North Glasgow, became the largest chemical plant in the world.
In 1824 Joseph Aspdin, a British brick layer turned builder, patented a chemical process for making portland cement which was an important advance in the building trades. This process involves sintering a mixture of clay and limestone to about 1400 °C, then grinding it into a fine powder which is then mixed with water, sand and gravel to produce concrete. Portland cement was used by the famous English engineer Marc Isambard Brunel several years later when constructing the Thames Tunnel.[28] Cement was used on a large scale in the construction of the London sewerage system a generation later.
The production of an alkali on a large scale became an important goal as well, and Nicolas Leblanc succeeded in 1791 in introducing a method for the production of sodium carbonate. The Leblanc process was a reaction of sulphuric acid with sodium chloride to give sodium sulphate and hydrochloric acid. The sodium sulphate was heated with limestone (calcium carbonate) and coal to give a mixture of sodium carbonate and calcium sulphide. Adding water separated the soluble sodium carbonate from the calcium sulphide. The process produced a large amount of pollution (the hydrochloric acid was initially vented to the air, and calcium sulphide was a useless waste product). Nonetheless, this synthetic soda ash proved economical compared to that from burning certain plants (barilla) or from kelp, which were the previously dominant sources of soda ash,[27] and also to potash (potassium carbonate) derived from hardwood ashes.
These two chemicals were very important because they enabled the introduction of a host of other inventions, replacing many small-scale operations with more cost-effective and controllable processes. Sodium carbonate had many uses in the glass, textile, soap, and paper industries. Early uses for sulphuric acid included pickling (removing rust) iron and steel, and for bleaching cloth.
The development of bleaching powder (calcium hypochlorite) by Scottish chemist Charles Tennant in about 1800, based on the discoveries of French chemist Claude Louis Berthollet, revolutionised the bleaching processes in the textile industry by dramatically reducing the time required (from months to days) for the traditional process then in use, which required repeated exposure to the sun in bleach fields after soaking the textiles with alkali or sour milk. Tennant's factory at St Rollox, North Glasgow, became the largest chemical plant in the world.
In 1824 Joseph Aspdin, a British brick layer turned builder, patented a chemical process for making portland cement which was an important advance in the building trades. This process involves sintering a mixture of clay and limestone to about 1400 °C, then grinding it into a fine powder which is then mixed with water, sand and gravel to produce concrete. Portland cement was used by the famous English engineer Marc Isambard Brunel several years later when constructing the Thames Tunnel.[28] Cement was used on a large scale in the construction of the London sewerage system a generation later.
Tuesday, June 3, 2008
Technological developments in Britain
TIn the early 18th century, British textile manufacture was based on wool which was processed by individual artisans, doing the spinning and weaving on their own premises. This system is called a cottage industry. Flax and cotton were also used for fine materials, but the processing was difficult because of the pre-processing needed, and thus goods in these materials made only a small proportion of the output.
Use of the spinning wheel and hand loom restricted the production capacity of the industry, but incremental advances increased productivity to the extent that manufactured cotton goods became the dominant British export by the early decades of the 19th century. India was displaced as the premier supplier of cotton goods.
Lewis Paul patented the Roller Spinning machine and the flyer-and-bobbin system for drawing wool to a more even thickness, developed with the help of John Wyatt in Birmingham. Paul and Wyatt opened a mill in Birmingham which used their new rolling machine powered by a donkey. In 1743, a factory was opened in Northampton with fifty spindles on each of five of Paul and Wyatt's machines. This operated until about 1764. A similar mill was built by Daniel Bourn in Leominster, but this burnt down. Both Lewis Paul and Daniel Bourn patented carding machines in 1748. Using two sets of rollers that travelled at different speeds, it was later used in the first cotton spinning mill. Lewis's invention was later developed and improved by Richard Arkwright in his water frame and Samuel Crompton in his spinning mule.
Other inventors increased the efficiency of the individual steps of spinning (carding, twisting and spinning, and rolling) so that the supply of yarn increased greatly, which fed a weaving industry that was advancing with improvements to shuttles and the loom or 'frame'. The output of an individual labourer increased dramatically, with the effect that the new machines were seen as a threat to employment, and early innovators were attacked and their inventions destroyed.
To capitalise upon these advances, it took a class of entrepreneurs, of which the most famous is Richard Arkwright. He is credited with a list of inventions, but these were actually developed by people such as Thomas Highs and John Kay; Arkwright nurtured the inventors, patented the ideas, financed the initiatives, and protected the machines. He created the cotton mill which brought the production processes together in a factory, and he developed the use of power — first horse power and then water power — which made cotton manufacture a mechanised industry. Before long steam power was applied to drive textile machineryextile manufacture
Use of the spinning wheel and hand loom restricted the production capacity of the industry, but incremental advances increased productivity to the extent that manufactured cotton goods became the dominant British export by the early decades of the 19th century. India was displaced as the premier supplier of cotton goods.
Lewis Paul patented the Roller Spinning machine and the flyer-and-bobbin system for drawing wool to a more even thickness, developed with the help of John Wyatt in Birmingham. Paul and Wyatt opened a mill in Birmingham which used their new rolling machine powered by a donkey. In 1743, a factory was opened in Northampton with fifty spindles on each of five of Paul and Wyatt's machines. This operated until about 1764. A similar mill was built by Daniel Bourn in Leominster, but this burnt down. Both Lewis Paul and Daniel Bourn patented carding machines in 1748. Using two sets of rollers that travelled at different speeds, it was later used in the first cotton spinning mill. Lewis's invention was later developed and improved by Richard Arkwright in his water frame and Samuel Crompton in his spinning mule.
Other inventors increased the efficiency of the individual steps of spinning (carding, twisting and spinning, and rolling) so that the supply of yarn increased greatly, which fed a weaving industry that was advancing with improvements to shuttles and the loom or 'frame'. The output of an individual labourer increased dramatically, with the effect that the new machines were seen as a threat to employment, and early innovators were attacked and their inventions destroyed.
To capitalise upon these advances, it took a class of entrepreneurs, of which the most famous is Richard Arkwright. He is credited with a list of inventions, but these were actually developed by people such as Thomas Highs and John Kay; Arkwright nurtured the inventors, patented the ideas, financed the initiatives, and protected the machines. He created the cotton mill which brought the production processes together in a factory, and he developed the use of power — first horse power and then water power — which made cotton manufacture a mechanised industry. Before long steam power was applied to drive textile machineryextile manufacture
Steam power
The development of the stationary steam engine was an essential early element of the Industrial Revolution; however, for most of the period of the Industrial Revolution, the majority of industries still relied on wind and water power as well as horse and man-power for driving small machines.
The first real attempt at industrial use of steam power was due to Thomas Savery in 1698. He constructed and patented in London a low-lift combined vacuum and pressure water pump, that generated about one horsepower (hp) and was used as in numerous water works and tried in a few mines (hence its "brand name", The miner's Friend), but it was not a success since it was limited in pumping height and prone to boiler explosions.
The first safe and successful steam power plant was introduced by Thomas Newcomen from 1719. Newcomen apparently conceived his machine quite independently of Savery, but as the latter had taken out a very wide-ranging patent, Newcomen and his associates were obliged to come to an arrangement with him, marketing the engine until 1733 under a joint patent.[26] Newcomen's engine appears to have been based on Papin's experiments carried out 30 years earlier, and employed a piston and cylinder, one end of which was open to the atmosphere above the piston. Steam just above atmospheric pressure (all that the boiler could stand) was introduced into the lower half of the cylinder beneath the piston during the gravity-induced upstroke; the steam was then condensed by a jet of cold water injected into the steam space to produce a partial vacuum; the pressure differential between the atmosphere and the vacuum on either side of the piston displaced it downwards into the cylinder, raising the opposite end of a rocking beam to which was attached a gang of gravity-actuated reciprocating force pumps housed in the mineshaft. The engine's downward power stroke raised the pump, priming it and preparing the pumping stroke. At first the phases were controlled by hand, but within ten years an escapement mechanism had been devised worked by of a vertical plug tree suspended from the rocking beam which rendered the engine self-acting.
A number of Newcomen engines were successfully put to use in Britain for draining hitherto unworkable deep mines, with the engine on the surface; these were large machines, requiring a lot of capital to build, and produced about 5 hp (3.7 kW). They were extremely inefficient by modern standards, but when located where coal was cheap at pit heads, opened up a great expansion in coal mining by allowing mines to go deeper. Despite their disadvantages, Newcomen engines were reliable and easy to maintain and continued to be used in the coalfields until the early decades of the nineteenth century. By 1729, when Newcomen died, his engines had spread to France, Germany, Austria, Hungary and Sweden. A total of 110 are known to have been built by 1733 when the joint patent expired, of which 14 were abroad. In the 1770s, the engineer John Smeaton built some very large examples and introduced a number of improvements. A total of 1,454 engines had been built by 1800.
A fundamental change in working principles was brought about by James Watt. With the close collaboration Matthew Boulton, he had succeeded by 1778 in perfecting his steam engine, which incorporated a series of radical improvements, notably the closing off of the upper part of the cylinder thereby making the low pressure steam drive the top of the piston instead of the atmosphere, use of a steam jacket and the celebrated separate steam condenser chamber. All this meant that a more constant temperature could be maintained in the cylinder and that engine efficiency no longer varied according to atmospheric conditions. These improvements increased engine efficiency by a factor of about five, saving 75% on coal costs.
Nor could the atmospheric engine be easily adapted to drive a rotating wheel, although Wasborough and Pickard did succeed in doing so towards 1780. However by 1783 the more economical Watt steam engine had been fully developed into a double-acting rotative type, which meant that it could be used to directly drive the rotary machinery of a factory or mill. Both of Watt's basic engine types were commercially very successful, and by 1800, the firm Boulton & Watt had constructed 496 engines, with 164 driving reciprocating pumps, 24 serving blast furnaces, and 308 powering mill machinery; most of the engines generated from 5 to 10 hp (7.5 kW).
The development of machine tools, such as the lathe, planing and shaping machines powered by these engines, enabled all the metal parts of the engines to be easily and accurately cut and in turn made it possible to build larger and more powerful engines.
Until about 1800, the most common pattern of steam engine was the beam engine, built as an integral part of a stone or brick engine-house, but soon various patterns of self-contained portative engines (readily removable, but not on wheels) were developed, such as the table engine. Towards the turn of the 19th century, the Cornish engineer Richard Trevithick, and the American, Oliver Evans began to construct higher pressure non-condensing steam engines, exhausting against the atmosphere. This allowed an engine and boiler to be combined into a single unit compact enough to be used on mobile road and rail locomotives and steam boats.
In the early 19th century after the expiration of Watt's patent, the steam engine underwent many improvements by a host of inventors and engineers.
The first real attempt at industrial use of steam power was due to Thomas Savery in 1698. He constructed and patented in London a low-lift combined vacuum and pressure water pump, that generated about one horsepower (hp) and was used as in numerous water works and tried in a few mines (hence its "brand name", The miner's Friend), but it was not a success since it was limited in pumping height and prone to boiler explosions.
The first safe and successful steam power plant was introduced by Thomas Newcomen from 1719. Newcomen apparently conceived his machine quite independently of Savery, but as the latter had taken out a very wide-ranging patent, Newcomen and his associates were obliged to come to an arrangement with him, marketing the engine until 1733 under a joint patent.[26] Newcomen's engine appears to have been based on Papin's experiments carried out 30 years earlier, and employed a piston and cylinder, one end of which was open to the atmosphere above the piston. Steam just above atmospheric pressure (all that the boiler could stand) was introduced into the lower half of the cylinder beneath the piston during the gravity-induced upstroke; the steam was then condensed by a jet of cold water injected into the steam space to produce a partial vacuum; the pressure differential between the atmosphere and the vacuum on either side of the piston displaced it downwards into the cylinder, raising the opposite end of a rocking beam to which was attached a gang of gravity-actuated reciprocating force pumps housed in the mineshaft. The engine's downward power stroke raised the pump, priming it and preparing the pumping stroke. At first the phases were controlled by hand, but within ten years an escapement mechanism had been devised worked by of a vertical plug tree suspended from the rocking beam which rendered the engine self-acting.
A number of Newcomen engines were successfully put to use in Britain for draining hitherto unworkable deep mines, with the engine on the surface; these were large machines, requiring a lot of capital to build, and produced about 5 hp (3.7 kW). They were extremely inefficient by modern standards, but when located where coal was cheap at pit heads, opened up a great expansion in coal mining by allowing mines to go deeper. Despite their disadvantages, Newcomen engines were reliable and easy to maintain and continued to be used in the coalfields until the early decades of the nineteenth century. By 1729, when Newcomen died, his engines had spread to France, Germany, Austria, Hungary and Sweden. A total of 110 are known to have been built by 1733 when the joint patent expired, of which 14 were abroad. In the 1770s, the engineer John Smeaton built some very large examples and introduced a number of improvements. A total of 1,454 engines had been built by 1800.
A fundamental change in working principles was brought about by James Watt. With the close collaboration Matthew Boulton, he had succeeded by 1778 in perfecting his steam engine, which incorporated a series of radical improvements, notably the closing off of the upper part of the cylinder thereby making the low pressure steam drive the top of the piston instead of the atmosphere, use of a steam jacket and the celebrated separate steam condenser chamber. All this meant that a more constant temperature could be maintained in the cylinder and that engine efficiency no longer varied according to atmospheric conditions. These improvements increased engine efficiency by a factor of about five, saving 75% on coal costs.
Nor could the atmospheric engine be easily adapted to drive a rotating wheel, although Wasborough and Pickard did succeed in doing so towards 1780. However by 1783 the more economical Watt steam engine had been fully developed into a double-acting rotative type, which meant that it could be used to directly drive the rotary machinery of a factory or mill. Both of Watt's basic engine types were commercially very successful, and by 1800, the firm Boulton & Watt had constructed 496 engines, with 164 driving reciprocating pumps, 24 serving blast furnaces, and 308 powering mill machinery; most of the engines generated from 5 to 10 hp (7.5 kW).
The development of machine tools, such as the lathe, planing and shaping machines powered by these engines, enabled all the metal parts of the engines to be easily and accurately cut and in turn made it possible to build larger and more powerful engines.
Until about 1800, the most common pattern of steam engine was the beam engine, built as an integral part of a stone or brick engine-house, but soon various patterns of self-contained portative engines (readily removable, but not on wheels) were developed, such as the table engine. Towards the turn of the 19th century, the Cornish engineer Richard Trevithick, and the American, Oliver Evans began to construct higher pressure non-condensing steam engines, exhausting against the atmosphere. This allowed an engine and boiler to be combined into a single unit compact enough to be used on mobile road and rail locomotives and steam boats.
In the early 19th century after the expiration of Watt's patent, the steam engine underwent many improvements by a host of inventors and engineers.
Mechanization
Richard Sutcliffe invented the first conveyor belt for use in coal mines in the early 1900s. Within the first forty years of the 20th century, there was an increase of over sixty percent in the amount of coal that was loaded mechanically rather than by man power1. Over time, less and less manual labour would be needed in the industry.
As this trend continued, the labor-intensive coal-mining methods that supported the miners declined. As the miners saw their livelihood taken away, resistance to mechanization grew. As noted in historian Keith Dix’s article, “What’s a Coal Miner to Do?” one of the first machines to arrive at West Virginia’s Kanawha field had to be escorted by armed guards. Dix also writes that “The same machine introduced at a mine in Illinois was operated at a slow speed because the superintendent feared labor troubles.” 1
Despite resistance, mechanization replaced more and more laborers. By 1940, almost seventy percent of coal loaded in West Virginia, one of the largest coal producing states, was done by machine.[1] With the increase of mechanization came hard times for the former miners and their families. Many miners moved to the cities to find work.
As this trend continued, the labor-intensive coal-mining methods that supported the miners declined. As the miners saw their livelihood taken away, resistance to mechanization grew. As noted in historian Keith Dix’s article, “What’s a Coal Miner to Do?” one of the first machines to arrive at West Virginia’s Kanawha field had to be escorted by armed guards. Dix also writes that “The same machine introduced at a mine in Illinois was operated at a slow speed because the superintendent feared labor troubles.” 1
Despite resistance, mechanization replaced more and more laborers. By 1940, almost seventy percent of coal loaded in West Virginia, one of the largest coal producing states, was done by machine.[1] With the increase of mechanization came hard times for the former miners and their families. Many miners moved to the cities to find work.
] Mining
source for the Coal has been used wAround 1842 coal became the main energy Industrial Revolution, the expanding railway system of countries being a prime user to power steam trains. Britain developed the main techniques of underground coal mining from the late 18th century onward with further progress being driven by 19th century and early 20th century progress.[1]
Because coal is found mainly underground, it must be mined or extracted prior to use. Large-scale coal mining developed during the Industrial Revolution, and coal provided the main source of primary energy for industry and transportation in the West from the 18th century to the 1950s. Coal remains an important energy source, due to its low cost and abundance when compared to other fuels, particularly for electricity generation.[2] However, coal is also mined today on a large scale by open pit methods wherever the coal strata strike the surface and is relatively shallow.
However oil and its associated fuels began to be used as alternative from this time onward. By the late 20th century coal was for the most part replaced in domestic as well as industrial and transportation usage by oil, natural gas or electricity produced from oil, gas, nuclear or renewable energy sources.
Since 1890, coal mining has also been a political and social issue. Coal miners' labour and trade unions became powerful in many countries in the 20th century, and often the miners were leaders of the Left or Socialist movements (as in Britain, Germany, Poland, Japan, Canada and the U.S.)[3] Since 1970, environmental issues have been increasingly important, including the health of miners, destruction of the landscape from strip mines and mountaintop removal, air pollution, and coal combustion's contribution to global warming.orldwide as a fuel for centuries.
Because coal is found mainly underground, it must be mined or extracted prior to use. Large-scale coal mining developed during the Industrial Revolution, and coal provided the main source of primary energy for industry and transportation in the West from the 18th century to the 1950s. Coal remains an important energy source, due to its low cost and abundance when compared to other fuels, particularly for electricity generation.[2] However, coal is also mined today on a large scale by open pit methods wherever the coal strata strike the surface and is relatively shallow.
However oil and its associated fuels began to be used as alternative from this time onward. By the late 20th century coal was for the most part replaced in domestic as well as industrial and transportation usage by oil, natural gas or electricity produced from oil, gas, nuclear or renewable energy sources.
Since 1890, coal mining has also been a political and social issue. Coal miners' labour and trade unions became powerful in many countries in the 20th century, and often the miners were leaders of the Left or Socialist movements (as in Britain, Germany, Poland, Japan, Canada and the U.S.)[3] Since 1970, environmental issues have been increasingly important, including the health of miners, destruction of the landscape from strip mines and mountaintop removal, air pollution, and coal combustion's contribution to global warming.orldwide as a fuel for centuries.
Metallurgy
The major change in the metal industries during the era of the Industrial Revolution was the replacement of organic fuels based on wood with fossil fuel based on coal. Much of this happened somewhat before the Industrial Revolution, based on innovations by Sir Clement Clerke and others from 1678, using coal reverberatory furnaces known as cupolas. These were operated by the flames, which contained carbon monoxide, playing on the ore and reducing the oxide to metal. This has the advantage that impurities (such as sulphur) in the coal do not migrate into the metal. This technology was applied to lead from 1678 and to copper from 1687. It was also applied to iron foundry work in the 1690s, but in this case the reverberatory furnace was known as an air furnace. The foundry cupola is a different (and later) innovation.
This was followed by Abraham Darby, who made great strides using coke to fuel his blast furnaces at Coalbrookdale in 1709. However, the coke pig iron he made was used mostly for the production of cast iron goods such as pots and kettles. He had the advantage over his rivals in that his pots, cast by his patented process, were thinner and cheaper than theirs. Coke pig iron was hardly used to produce bar iron in forges until the mid 1750s, when his son Abraham Darby II built Horsehay and Ketley furnaces (not far from Coalbrookdale). By then, coke pig iron was cheaper than charcoal pig iron.
Bar iron for smiths to forge into consumer goods was still made in finery forges, as it long had been. However, new processes were adopted in the ensuing years. The first is referred to today as potting and stamping, but this was superseded by Henry Cort's puddling process. From 1785, perhaps because the improved version of potting and stamping was about to come out of patent, a great expansion in the output of the British iron industry began. The new processes did not depend on the use of charcoal at all and were therefore not limited by charcoal sources.
Up to that time, British iron manufacturers had used considerable amounts of imported iron to supplement native supplies. This came principally from Sweden from the mid 17th century and later also from Russia from the end of the 1720s. However, from 1785, imports decreased because of the new iron making technology, and Britain became an exporter of bar iron as well as manufactured wrought iron consumer goods.
Since iron was becoming cheaper and more plentiful, it also became a major structural material following the building of the innovative Iron Bridge in 1778 by Abraham Darby III.
An improvement was made in the production of steel, which was an expensive commodity and used only where iron would not do, such as for the cutting edge of tools and for springs. Benjamin Huntsman developed his crucible steel technique in the 1740s. The raw material for this was blister steel, made by the cementation process.
The supply of cheaper iron and steel aided the development of boilers and steam engines, and eventually railways. Improvements in machine tools allowed better working of iron and steel and further boosted the industrial growth of Britain
This was followed by Abraham Darby, who made great strides using coke to fuel his blast furnaces at Coalbrookdale in 1709. However, the coke pig iron he made was used mostly for the production of cast iron goods such as pots and kettles. He had the advantage over his rivals in that his pots, cast by his patented process, were thinner and cheaper than theirs. Coke pig iron was hardly used to produce bar iron in forges until the mid 1750s, when his son Abraham Darby II built Horsehay and Ketley furnaces (not far from Coalbrookdale). By then, coke pig iron was cheaper than charcoal pig iron.
Bar iron for smiths to forge into consumer goods was still made in finery forges, as it long had been. However, new processes were adopted in the ensuing years. The first is referred to today as potting and stamping, but this was superseded by Henry Cort's puddling process. From 1785, perhaps because the improved version of potting and stamping was about to come out of patent, a great expansion in the output of the British iron industry began. The new processes did not depend on the use of charcoal at all and were therefore not limited by charcoal sources.
Up to that time, British iron manufacturers had used considerable amounts of imported iron to supplement native supplies. This came principally from Sweden from the mid 17th century and later also from Russia from the end of the 1720s. However, from 1785, imports decreased because of the new iron making technology, and Britain became an exporter of bar iron as well as manufactured wrought iron consumer goods.
Since iron was becoming cheaper and more plentiful, it also became a major structural material following the building of the innovative Iron Bridge in 1778 by Abraham Darby III.
An improvement was made in the production of steel, which was an expensive commodity and used only where iron would not do, such as for the cutting edge of tools and for springs. Benjamin Huntsman developed his crucible steel technique in the 1740s. The raw material for this was blister steel, made by the cementation process.
The supply of cheaper iron and steel aided the development of boilers and steam engines, and eventually railways. Improvements in machine tools allowed better working of iron and steel and further boosted the industrial growth of Britain
Transfer of knowledge
Another means for the spread of innovation was by the network of informal philosophical societies, like the Lunar Society of Birmingham, in which members met to discuss 'natural philosophy' (i.e. science) and often its application to manufacturing. The Lunar Society flourished from 1765 to 1809, and it has been said of them, "They were, if you like, the revolutionary committee of that most far reaching of all the eighteenth century revolutions, the Industrial Revolution".[25] Other such societies published volumes of proceedings and transactions. For example, the London-based Royal Society of Arts published an illustrated volume of new inventions, as well as papers about them in its annual Transactions.
There were publications describing technology. Encyclopaedias such as Harris's Lexicon Technicum (1704) and Dr Abraham Rees's Cyclopaedia (1802-1819) contain much of value. Cyclopaedia contains an enormous amount of information about the science and technology of the first half of the Industrial Revolution, very well illustrated by fine engravings. Foreign printed sources such as the Descriptions des Arts et Métiers and Diderot's Encyclopédie explained foreign methods with fine engraved plates.
Periodical publications about manufacturing and technology began to appear in the last decade of the 18th century, and many regularly included notice of the latest patents. Foreign periodicals, such as the Annales des Mines, published accounts of travels made by French engineers who observed British methods on study tours.
There were publications describing technology. Encyclopaedias such as Harris's Lexicon Technicum (1704) and Dr Abraham Rees's Cyclopaedia (1802-1819) contain much of value. Cyclopaedia contains an enormous amount of information about the science and technology of the first half of the Industrial Revolution, very well illustrated by fine engravings. Foreign printed sources such as the Descriptions des Arts et Métiers and Diderot's Encyclopédie explained foreign methods with fine engraved plates.
Periodical publications about manufacturing and technology began to appear in the last decade of the 18th century, and many regularly included notice of the latest patents. Foreign periodicals, such as the Annales des Mines, published accounts of travels made by French engineers who observed British methods on study tours.
Monday, June 2, 2008
Marxism
Marxism is essentially a reaction to the Industrial Revolution.[37] According to Karl Marx, industrialisation polarised society into the bourgeoisie (those who own the means of production, the factories and the land) and the much larger proletariat (the working class who actually perform the labour necessary to extract something valuable from the means of production). He saw the industrialisation process as the logical dialectical progression of feudal economic modes, necessary for the full development of capitalism, which he saw as in itself a necessary precursor to the development of socialism and eventually communism
Sunday, June 1, 2008
Romanticism
During the Industrial Revolution an intellectual and artistic hostility towards the new industrialisation developed. This was known as the Romantic movement. Its major exponents in English included the artist and poet William Blake and poets William Wordsworth, Samuel Taylor Coleridge, John Keats, Byron and Percy Bysshe Shelley. The movement stressed the importance of "nature" in art and language, in contrast to 'monstrous' machines and factories; the "Dark satanic mills" of Blake's poem And did those feet in ancient time. Mary Shelley's short story Frankenstein reflected concerns that scientific progress might be two-edged.
Industrial Revolution
The Industrial Revolution was a period in the late 18th and early 19th centuries when major changes in agriculture, manufacturing, and transportation had a profound effect on the socioeconomic and cultural conditions in Britain. The changes subsequently spread throughout Europe and North America and eventually the world, a process that continues as industrialisation. The onset of the Industrial Revolution marked a major turning point in human society; almost every aspect of daily life was eventually influenced in some way. In the later part of the 1700s the manual labour-based economy of some parts of Great Britain began to be replaced by one dominated by the manufacture by machinery. It started with the mechanisation of the textile industries, the development of iron-making techniques and the increased use of refined coal. Trade expansion was enabled by the introduction of canals, improved roads and railways. The introduction of steam power (fuelled primarily by coal) and powered machinery (mainly in textile manufacturing) underpinned the dramatic increases in production capacity.[2] The development of all-metal machine tools in the first two decades of the 19th century facilitated the manufacture of more production machines for manufacturing in other industries. The effects spread throughout Western Europe and North America during the 19th century, eventually affecting most of the world. The impact of this change on society was enormous.[3]
The First Industrial Revolution, which began in the eighteenth century merged into the Second Industrial Revolution around 1850, when technological and economic progress gained momentum with the development of steam-powered ships, railways, and later in the nineteenth century with the internal combustion engine and electrical power generation.
The period of time covered by the Industrial Revolution varies with different historians. Eric Hobsbawm held that it 'broke out' in the 1780s and was not fully felt until the 1830s or 1840s,[4] while T. S. Ashton held that it occurred roughly between 1760 and 1830.[5] Some twentieth century historians such as John Clapham and Nicholas Crafts have argued that the process of economic and social change took place gradually and the term revolution is not a true description of what took place. This is still a subject of debate amongst historians.[6][7]
GDP per capita was broadly stable before the Industrial Revolution and the emergence of the modern capitalist economy.[8] The Industrial Revolution began an era of per-capita economic growth in capitalist economies.[
The First Industrial Revolution, which began in the eighteenth century merged into the Second Industrial Revolution around 1850, when technological and economic progress gained momentum with the development of steam-powered ships, railways, and later in the nineteenth century with the internal combustion engine and electrical power generation.
The period of time covered by the Industrial Revolution varies with different historians. Eric Hobsbawm held that it 'broke out' in the 1780s and was not fully felt until the 1830s or 1840s,[4] while T. S. Ashton held that it occurred roughly between 1760 and 1830.[5] Some twentieth century historians such as John Clapham and Nicholas Crafts have argued that the process of economic and social change took place gradually and the term revolution is not a true description of what took place. This is still a subject of debate amongst historians.[6][7]
GDP per capita was broadly stable before the Industrial Revolution and the emergence of the modern capitalist economy.[8] The Industrial Revolution began an era of per-capita economic growth in capitalist economies.[
Are men good listeners?
There are different kinds of men – some good listeners, some bad. I think I’m a very bad listener – I’d put myself in that category. Some men are so stressed out over problems in their own lives, that they just switch off. They might actually like to listen to their partner, but they’re so caught up in their own problems that they can’t, and then the women complain. They’re so caught up in their own issues that even though they love their partner, they’re unable to hear them out patiently. There are also men who are very giving and patient as listeners, but then again, there are others who just don’t have the right intention. Sometimes, they’re just interested in sex or a short-term relationship, so they don’t invest in being a good listener. I would count myself as a bad listener because again – I’m so busy and so caught up with my own problems that if I had a girlfriend, I’d make a for a very bad listener! Riddhima Kapoor Sahni Entrepreneur Well, it is tough to answer this one. Men do listen, but only when they want to. If it is a topic of their concern then they are all ears. For instance, if you discuss how many runs did the Jaipur IPL team score then they would be all game to even discuss the rating of the different teams. But if you are planning to discuss shopping, then you will get excuses. And knowing this now, I know how to make my hubby listen to me. I try and talk about cricket that he is crazy about and then eventually talk about my shopping plans. So, a good dose of your guy’s favourite topic will get him listening, trust me! As far as I am concerned, when it comes to listening, I’m a bit of a hyper girl. In fact, I’d say, I’m quite impatient. And with me too, it has to be a subject of my interest. And that’s how my husband gets me to listen to him as well. So we balance each other out quite well.
Saturday, May 31, 2008
Statement
ATTENTION TECHNICIANS:Update your skills in WELDING. Welding training courses are being offered through Continuing Education .
Choose from a variety of welding processes. Students select the type of welding they wish to learn at the first class session or in a meeting with the instructor prior to the first day of class.
Classes offered
Oxyacetylene Welding
Intro to Combination Welding
Arc Welding I, II
Intro to Gas Metal Arc Welding
Structural Welding I, II, III
Pipe Welding I, II
Gas Metal Arc Welding
Intro to Gas Tungsten Arc Welding
Flux Cored Arc Welding
Gas Tungsten Arc Welding
Classes are offered day and night, and are competency based. This means you work at your own pace.
Texas State Technical College will train welders to companies requirements and specifications.
Continuing Education courses are based on satisfactory completion of all competencies and/or up to 80 hours of instruction. High School diploma or GED not required. Qualified and bilingual instructors are on hand to meet your teaching needs.
First-come, first-served, limited enrollment!
Choose from a variety of welding processes. Students select the type of welding they wish to learn at the first class session or in a meeting with the instructor prior to the first day of class.
Classes offered
Oxyacetylene Welding
Intro to Combination Welding
Arc Welding I, II
Intro to Gas Metal Arc Welding
Structural Welding I, II, III
Pipe Welding I, II
Gas Metal Arc Welding
Intro to Gas Tungsten Arc Welding
Flux Cored Arc Welding
Gas Tungsten Arc Welding
Classes are offered day and night, and are competency based. This means you work at your own pace.
Texas State Technical College will train welders to companies requirements and specifications.
Continuing Education courses are based on satisfactory completion of all competencies and/or up to 80 hours of instruction. High School diploma or GED not required. Qualified and bilingual instructors are on hand to meet your teaching needs.
First-come, first-served, limited enrollment!
Welding Technology Curriculum
At TSTC, we believe students need to know not only how welding processes work, but also why certain welding processes are used. At TSTC we offer all processes needed in the welding industry workforce.
Welding Technology Job Placement
Students from Welding Technology are prepared for employment and are assured a job in the welding industry.
100% + job placement rate
Keppel AmFELS
Tri-Pak
Walzel & Associates, Inc.
Benders Ship Builders
Bay LTD
IWS
A.D. Welding
Entry Level Salary Range
Entry level pay rate ranges from $12.00 to $15.00 per hour and $40.00 to $50.00 per-diem, and there is always plenty of overtime available.
Average starting salary - $30,000-35,000
100% + job placement rate
Keppel AmFELS
Tri-Pak
Walzel & Associates, Inc.
Benders Ship Builders
Bay LTD
IWS
A.D. Welding
Entry Level Salary Range
Entry level pay rate ranges from $12.00 to $15.00 per hour and $40.00 to $50.00 per-diem, and there is always plenty of overtime available.
Average starting salary - $30,000-35,000
Welding Technology Facilities
The Texas State Technical College Harlingen is a modern 167.8 acre campus consisting of 24 instructional facilities equipped for learning with state of the art, industry standard equipment and laboratories to help prepare employees for tomorrow’s careers, helping to strengthen the economic competitiveness of Texas and improve the lives of its people.
Career Outlook
The entry-level pay for welders ranges $12 to $15 per hour, plus $40 to $50 per diem pay. Most graduates report that plenty of overtime is available in the industry, so the average annual salary stands at $30,000 to $35,000. It’s a financially attractive pay scale, considering you could earn the Certificate of Completion in three semesters.
Friday, May 30, 2008
Welding Technology
WHY UM-HELENA?
The UM-Helena Welding Technology program offers students the opportunity to train on the newest welding equipment available in the industry. As a regional training center for Miller Electric, UM-Helena receives the latest, state-of-the-art Miller welding equipment. Miller trains our instructors to use this equipment and, in turn, our instructors pass this knowledge on to you, our student. Our instructors have spent many years actually working in the trade and know the demands of the industry first-hand.
WHAT CAN I LEARN?
UM-Helena’s Welding Technology program teaches welding skills using oxyacetylene, manual stick electrode, semiautomatic Mig, Tig (Heliarc), Pulse Mig, and various other welding processes. Working from blueprints, students follow exact specifications and apply practical shop math to accomplish required tasks. Students complete live work projects using skills acquired in classes. In addition, students have the option to take the American Welding Society (AWS) certification practical exams. Our Welding program provides students with the knowledge and training necessary to successfully complete AWS certifications in Stick, Mig, and Tig processes. Certified AWS inspectors approve each test, which is recognized worldwide as the standard to measure welding competence. In 2005, UM-Helena students attained an impressive 98.9% passing rate on their AWS certification tests.
WHERE CAN THIS TAKE ME?
Welders are needed throughout the world, making the job opportunities endless. Students enter the work force with a wide variety of skills and can specialize in specific aspects of the welding trade, including layout and inspection welding, new construction welding, and fabrication.
HOW CAN I EARN MY DEGREE?
Students may choose a one-year certificate in Welding Technology or a two-year Associate of Applied Science degree in Metals Technology. The second year of the AAS degree in Metals Technology focuses on learning machine tool skills. The one-year Welding Technology Certificate of Completion is scheduled as a block of daytime classes and includes the following coursework
Career Outlook
The entry-level pay for welders ranges $12 to $15 per hour, plus $40 to $50 per diem pay. Most graduates report that plenty of overtime is available in the industry, so the average annual salary stands at $30,000 to $35,000. It’s a financially attractive pay scale, considering you could earn the Certificate of Completion in three semesters.
Welding Technology
Students in the Welding Technology department undergo hands-on training on the same equipment used by industry. They learn to use various welding processes including oxyacetylene gas welding, gas tungsten arc, gas metal arc and other sophisticated processes. They also learn to perform welding in all positions with fillet and groove welds, and to plan, design and fabricate welded projects. Students are offered a three-semester Certificate of Completion program.
Thursday, May 29, 2008
SINK OR SURVIVE: THE REVERSAL OF A VOCATIONAL METALS PROGRAM
full time vocational technical school with students learning, preparing and planning on careers and higher education in several areas of both technical trades and related technical areas which includes: nursing, graphic arts, digital media, technical drawing (draftsmen), machine shop, cosmetology, printing, auto tech/auto body, as well as all of the building trade areas which includes our program of Metal Fabrication / Welding.
Eight years ago, our metal fabrication program was tanked, stalled, sinking, and preparing to close its doors for good. At that time, I was a newly hired teacher and looking outward, upward and forward in any possible direction to improve our program. Basically, it was survival.
CURRICULUM
I asked our school's leadership and advisory committee members to begin a creative blacksmith program proponent to our metal fabrication program. With the school’s approval, I needed a small amount of money ($2,000) to purchase equipment to include a forge, used anvils, used post vices and hand tools. In addition, the school sent me and my fellow teacher to professional development training during our summers to learn blacksmithing, metallurgy, safety, welding, welding inspection, etc. This initiated our success and was start of reversing that downward spiral of our program.
COMMITMENT
I like to borrow the use of the naval statement, “It takes five miles to turn around an aircraft carrier,” and it also takes a few years to turn around a metal fabrication program. In our case, it took a large commitment, hard work, long hours and summers to make our program succeed. In a short time, however, I could not believe my eyes when we witnessed our students becoming more creative, really having fun, and maintaining a strong passion in making their projects. It was like magic!
Blacksmithing has such a deep and rich heritage in our country’s history and still has a way of inspiring and shaping the next generation of young adults who are interested in metal working. My hat is off to our school’s leadership for their support and to the local New England blacksmiths (N.E.B.) that helped me get our program jump-started. N.E.B. played a large part in supporting, encouraging and mentoring our teachers and program.
My Background
I include this because I feel it plays a large part in my success and in the success of this program. I came from a family of union structural ironworkers from New York City and Philadelphia. It was an honor to be a metal worker in my family.
As a little boy, I grew up listening to my father, grandfather, and all of my uncles talk about erecting some of the greatest landmarks in our country, such as bridges, skyscrapers, and tunnels both in NYC and Philadelphia. Some of these structures included the following: George Washington Bridge, Triborough Bridge, Empire State Building, Pam- Am Building, Chrysler Building, Brooklyn Battery Tunnel, Verazano Narrows Bridge, Twin Towers, Delaware Memorial Bridge, and so many other bridges, tunnels and skyscrapers that have since escaped my memory. Like my father, I too became a union ironworker in NYC and continued my family’s heritage.
My teaching partner, Mark Chludenski, was a union boilermaker (folks that build power plants) from Massachusetts and, like me, his father and brother were both boilermakers. His family had a great sense of pride, craftsmanship, and above all, honored to be metal workers. As teachers, our similar backgrounds inspired us to get along very well together. We both teach our students pride in welding and metal fabrication.
SAFETY Our trade area, as well as other areas in our school or any other technical school in the country, can be inherently dangerous if safety is not followed. However, safety is one of strongest taught lessons across the board in all of our programs with sound, mindful, and clearly understood personal protection along with instruction on how to work safely with others, both in school and upon graduation.
During our summer professional development training, Assabet teachers are certified as OSHA (Occupational Safety and Health Administration) safety instructors. We have not had any serious accidents in all the years of teaching. This is largely due to a never ending emphasis on safety, safety, and more safety.
I have worked as an Ironworker, pipe welder, sheet metal worker and have been in many dangerous working conditions, but always remembered my own personal safety and safety for my fellow workers. I have never been injured in an accident in over 25 years of metal working.
The backbone of success
The real “nuts and bolts” in how our blacksmith program got off the ground was largely due to a strong backing and support from our school's top leadership, starting with the school's superintendent, principal, vocational chairmen and, above all, the school’s level of commitment.
Also, we have a strong program advisory committee that meets several times a year after school. This committee is made up of professional men and women who are welders, sheet metal workers, blacksmiths, engineers, metallurgists, metal fabrication shop owners, welding salesmen, metal artists, and union apprenticeship teachers. It's a great blend of metal workers.
Our school's leadership is one that believes and is built on leading by example, working hard and letting their teachers succeed by allowing them to create and drive their programs with successful results.
The approach
Our teachers and students have made several presentations throughout the years to the evening meetings of Assabet school’s committee with our students both demonstrating their talents and presenting their views related to community service projects using blacksmithing, as well as how much they enjoy forging and creating functional and artistic metal art. At the end of the day, blacksmithing is a way for kids to have fun and make neat metal stuff to bring home to their families to admire and appreciate, while still learning about how to move metal and see what happens to metal when you heat it, form it, bend it, and weld it.
AN interesting blend
Blending technical skills with fun, our students learn the essentials of metal fabrication that include: blueprint reading, shop math, welding and sheet metal fabrication, which is mandated by the curriculum framework of the State of Massachusetts. They also learn about the opportunities open to them beyond high school, whether it be furthering their education at a school such as Hobart Institute or going directly into the world of work. However, our students have fun with hot metal along the way.
I believe if you make your high school metal fabrication and welding programs fun and exciting, you can bring your students to the next level of learning by teaching them the art of technical skills, passion for learning, and essential skills to become successful in life. Our success has been built on good old-fashioned hard work, dedication, and a willingness to succeed.
Neil Mansfield is Metal Fabrication Teacher at Assabet Valley Vocational High School and a graduate of the Combination Structural and Pipe Welding Program at Hobart In
Eight years ago, our metal fabrication program was tanked, stalled, sinking, and preparing to close its doors for good. At that time, I was a newly hired teacher and looking outward, upward and forward in any possible direction to improve our program. Basically, it was survival.
CURRICULUM
I asked our school's leadership and advisory committee members to begin a creative blacksmith program proponent to our metal fabrication program. With the school’s approval, I needed a small amount of money ($2,000) to purchase equipment to include a forge, used anvils, used post vices and hand tools. In addition, the school sent me and my fellow teacher to professional development training during our summers to learn blacksmithing, metallurgy, safety, welding, welding inspection, etc. This initiated our success and was start of reversing that downward spiral of our program.
COMMITMENT
I like to borrow the use of the naval statement, “It takes five miles to turn around an aircraft carrier,” and it also takes a few years to turn around a metal fabrication program. In our case, it took a large commitment, hard work, long hours and summers to make our program succeed. In a short time, however, I could not believe my eyes when we witnessed our students becoming more creative, really having fun, and maintaining a strong passion in making their projects. It was like magic!
Blacksmithing has such a deep and rich heritage in our country’s history and still has a way of inspiring and shaping the next generation of young adults who are interested in metal working. My hat is off to our school’s leadership for their support and to the local New England blacksmiths (N.E.B.) that helped me get our program jump-started. N.E.B. played a large part in supporting, encouraging and mentoring our teachers and program.
My Background
I include this because I feel it plays a large part in my success and in the success of this program. I came from a family of union structural ironworkers from New York City and Philadelphia. It was an honor to be a metal worker in my family.
As a little boy, I grew up listening to my father, grandfather, and all of my uncles talk about erecting some of the greatest landmarks in our country, such as bridges, skyscrapers, and tunnels both in NYC and Philadelphia. Some of these structures included the following: George Washington Bridge, Triborough Bridge, Empire State Building, Pam- Am Building, Chrysler Building, Brooklyn Battery Tunnel, Verazano Narrows Bridge, Twin Towers, Delaware Memorial Bridge, and so many other bridges, tunnels and skyscrapers that have since escaped my memory. Like my father, I too became a union ironworker in NYC and continued my family’s heritage.
My teaching partner, Mark Chludenski, was a union boilermaker (folks that build power plants) from Massachusetts and, like me, his father and brother were both boilermakers. His family had a great sense of pride, craftsmanship, and above all, honored to be metal workers. As teachers, our similar backgrounds inspired us to get along very well together. We both teach our students pride in welding and metal fabrication.
SAFETY Our trade area, as well as other areas in our school or any other technical school in the country, can be inherently dangerous if safety is not followed. However, safety is one of strongest taught lessons across the board in all of our programs with sound, mindful, and clearly understood personal protection along with instruction on how to work safely with others, both in school and upon graduation.
During our summer professional development training, Assabet teachers are certified as OSHA (Occupational Safety and Health Administration) safety instructors. We have not had any serious accidents in all the years of teaching. This is largely due to a never ending emphasis on safety, safety, and more safety.
I have worked as an Ironworker, pipe welder, sheet metal worker and have been in many dangerous working conditions, but always remembered my own personal safety and safety for my fellow workers. I have never been injured in an accident in over 25 years of metal working.
The backbone of success
The real “nuts and bolts” in how our blacksmith program got off the ground was largely due to a strong backing and support from our school's top leadership, starting with the school's superintendent, principal, vocational chairmen and, above all, the school’s level of commitment.
Also, we have a strong program advisory committee that meets several times a year after school. This committee is made up of professional men and women who are welders, sheet metal workers, blacksmiths, engineers, metallurgists, metal fabrication shop owners, welding salesmen, metal artists, and union apprenticeship teachers. It's a great blend of metal workers.
Our school's leadership is one that believes and is built on leading by example, working hard and letting their teachers succeed by allowing them to create and drive their programs with successful results.
The approach
Our teachers and students have made several presentations throughout the years to the evening meetings of Assabet school’s committee with our students both demonstrating their talents and presenting their views related to community service projects using blacksmithing, as well as how much they enjoy forging and creating functional and artistic metal art. At the end of the day, blacksmithing is a way for kids to have fun and make neat metal stuff to bring home to their families to admire and appreciate, while still learning about how to move metal and see what happens to metal when you heat it, form it, bend it, and weld it.
AN interesting blend
Blending technical skills with fun, our students learn the essentials of metal fabrication that include: blueprint reading, shop math, welding and sheet metal fabrication, which is mandated by the curriculum framework of the State of Massachusetts. They also learn about the opportunities open to them beyond high school, whether it be furthering their education at a school such as Hobart Institute or going directly into the world of work. However, our students have fun with hot metal along the way.
I believe if you make your high school metal fabrication and welding programs fun and exciting, you can bring your students to the next level of learning by teaching them the art of technical skills, passion for learning, and essential skills to become successful in life. Our success has been built on good old-fashioned hard work, dedication, and a willingness to succeed.
Neil Mansfield is Metal Fabrication Teacher at Assabet Valley Vocational High School and a graduate of the Combination Structural and Pipe Welding Program at Hobart In
BE THE SOLUTION… NOT THE PROBLEM
The media has, in recent times, been abundantly reporting about the shortage of skilled labor and, in particular, the shortage of welders. Much of this shortage is due to the retirement of the “baby boomer” generation. If this projected increasing shortage of skilled welders cannot be resolved, it is bound to have a dramatic effect on our economy. Why? Because welding is used to join all the commercial metals and alloys of different types and strengths.
Welding is vital to our national economy and the defense of our nation. It is often said that more than 50% of the country’s gross national product is related to welding in one way or another. This is why a shortage of this important trade may potentially have a significant negative impact on our economy.
The American Welding Society has started a ten million dollar capital campaign, Welding for the Strength of America, which includes a welder workforce development program. The National Science Foundation has provided $4.9 million to establish a National Center for Welding Education and Training. There are probably many more initiatives taking place around the country to help reduce this shortage, which has been estimated to be around 200,000 by 2010.
Please note the Unemployment Rates graph that shows unemployment in selected states and there is a line that shows the nationwide unemployment rate. Unemployment is on the increase again. Nationwide, there are over seven million people unemployed. The welding industry needs 200,000 welders. This represents 2.8% of the total unemployment number. It seems that somehow, there should be a way to convince at least 2.8 percent of unemployed people that welders are needed and that welding pays well. If it were possible to FOCUS financial and human resources towards this small percentage of unemployed, the shortage could be virtually eliminated.
You can help! Our research shows that one of the most effective ways to let others know about welding opportunities is through word of mouth. If each of you who read this article tell your friends and your children about this amazing opportunity and encourage them to spread the word, the shortage could be greatly alleviated.
Companies can help by financially supporting the American Welding Society’s campaign and by spreading the word through their corporate advertising methods and employee newsletters. They can also contribute by offering competitive wages to employees with talents and skills. Schools can help by maintaining welding programs and promoting these classes to youth and area industry. It may also be helpful if the amount of available regional welder training would be more in line with the population of welders in the region. According to information available to me, in the state of Connecticut there is one welding school supporting a workforce of almost 3,000 welders whilst on the other extreme, there are 125 welding schools in Kentucky, supporting a workforce of over 8,000 welders, which is a ratio of 69 welders per welding school.
This nation was founded on innovation. This worker shortage is not an overwhelming problem and it can be solved through cooperation. If you have ideas to share, let us know. Think about being part of the solution!
Welding is vital to our national economy and the defense of our nation. It is often said that more than 50% of the country’s gross national product is related to welding in one way or another. This is why a shortage of this important trade may potentially have a significant negative impact on our economy.
The American Welding Society has started a ten million dollar capital campaign, Welding for the Strength of America, which includes a welder workforce development program. The National Science Foundation has provided $4.9 million to establish a National Center for Welding Education and Training. There are probably many more initiatives taking place around the country to help reduce this shortage, which has been estimated to be around 200,000 by 2010.
Please note the Unemployment Rates graph that shows unemployment in selected states and there is a line that shows the nationwide unemployment rate. Unemployment is on the increase again. Nationwide, there are over seven million people unemployed. The welding industry needs 200,000 welders. This represents 2.8% of the total unemployment number. It seems that somehow, there should be a way to convince at least 2.8 percent of unemployed people that welders are needed and that welding pays well. If it were possible to FOCUS financial and human resources towards this small percentage of unemployed, the shortage could be virtually eliminated.
You can help! Our research shows that one of the most effective ways to let others know about welding opportunities is through word of mouth. If each of you who read this article tell your friends and your children about this amazing opportunity and encourage them to spread the word, the shortage could be greatly alleviated.
Companies can help by financially supporting the American Welding Society’s campaign and by spreading the word through their corporate advertising methods and employee newsletters. They can also contribute by offering competitive wages to employees with talents and skills. Schools can help by maintaining welding programs and promoting these classes to youth and area industry. It may also be helpful if the amount of available regional welder training would be more in line with the population of welders in the region. According to information available to me, in the state of Connecticut there is one welding school supporting a workforce of almost 3,000 welders whilst on the other extreme, there are 125 welding schools in Kentucky, supporting a workforce of over 8,000 welders, which is a ratio of 69 welders per welding school.
This nation was founded on innovation. This worker shortage is not an overwhelming problem and it can be solved through cooperation. If you have ideas to share, let us know. Think about being part of the solution!
Subscribe to:
Posts (Atom)